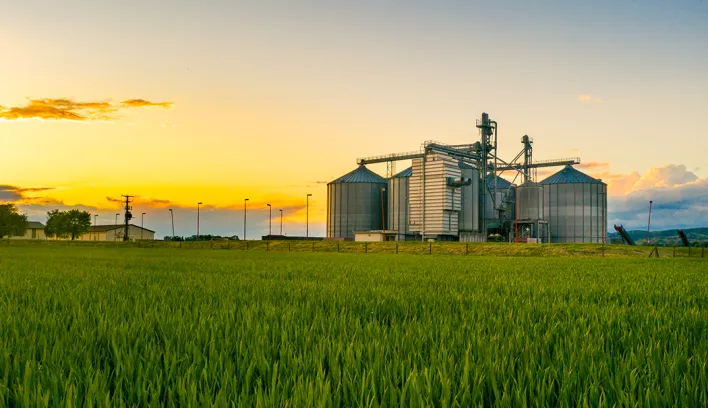
Comment ces trois entreprises industrielles électrifient leurs process pour plus de sobriété
Avec plus de 100 térawattheures par an, l’industrie représente environ 25 % de la consommation finale d’électricité en France. Un poste de dépense énergétique colossal, mais aussi un formidable levier de décarbonation. Car si elle reste historiquement dépendante des énergies fossiles, l’industrie dispose aujourd’hui de solutions concrètes pour accélérer sa transition : électrification des procédés, pilotage intelligent de la consommation, recours à des dispositifs d’effacement ou à des équipements moins énergivores. Cette cinquième saison d’Un Pas de Plus, série vidéo produite par Bpifrance, met en lumière trois entreprises membres de la Communauté du Coq Vert qui, chacune à leur manière, ont engagé cette transformation. De la gestion fine des usages à la substitution des énergies, elles prouvent que l’optimisation énergétique et la décarbonation peuvent aller de pair.
Setforge : électrifier pour contrer les effets de la crise du gaz
À L’Horme, dans la Loire, Setforge transforme le métal à haute température pour produire des pièces destinées à l’automobile, à l’aéronautique ou encore à la filière BTP. Une activité énergivore par nature, que l’entreprise choisit d’adapter à marche forcée. “Nous avons un seul credo, celui de choisir notre transition et de ne pas la subir”, insiste Marie Siméon, cheffe de projet décarbonation. Ce caractère proactif prend toute sa signification face à l’urgence climatique d’une part et face aux tensions géopolitiques internationales d’autre part, ces dernières ayant eu pour conséquence l’explosion du prix du gaz et la crainte d’une perte de souveraineté énergétique. Pour renforcer sa résilience, Setforge s’est décidée à investir. “Nous avons pour projet d’électrifier d’ici deux ans une ligne de traitement thermique, dont les fours fonctionnent initialement au gaz. Quatre des cinq fours actuellement en service sont concernés, ce qui occasionnerait une économie d’environ 800 tonnes équivalent CO₂, dévoile Didier Forestier, directeur général de l’entreprise. Pour augmenter ces résultats, nous prévoyons aussi d’installer des panneaux solaires sur l’ensemble de nos toitures, soit une surface de 15 000m².” Chez Setforge, la transition passe aussi par une multitude de “quick-wins” : passage à l’éclairage LED, installation de compteurs connectés pour piloter la consommation en temps réel, ou encore intégration du sujet dans la culture de l’entreprise. “C’est un vrai challenge. C’est aux dirigeants de donner l’exemple : l’escalier se balaye toujours par le haut. On met un accent particulier sur la communication et sur les enjeux afin qu’ils soient compris par l’ensemble des salariés”, conclut Didier Forestier.
STF Imprimeries : efficacité et rigueur dans une industrie électro-intensive
Chez STF Imprimeries, on imprime des millions de documents chaque mois dans toute la France. Et la consommation énergétique s’en ressent. “Nous consommons 23 GWhs d’électricité et 18 GWhs de gaz par an. Il nous a fallu nous mobiliser pour faire le maximum d’économies, ne serait-ce que pour protéger nos clients et limiter nos augmentations de prix”, résume Hadrien Miailhé, responsable du site BLG-Toul en Lorraine. Depuis plusieurs années, l’entreprise transforme ses équipements : pilotage de la consommation d’électricité, remplacement progressif des machines, gestion optimisée de l’air comprimé, mesures en temps réel… “On vise l’usine 3.0. Grâce à nos efforts, on a réduit notre consommation électrique de 40 % en trois ans”, se félicite Carole Leveaux-Coïc, directrice générale adjointe. Certes, l’intégration du photovoltaïque semble peu pertinente ici (à peine 5 % de la consommation couverte) mais d’autres solutions existent. La chaleur dégagée par les sécheurs est notamment réutilisée pour chauffer les locaux, et des contrats d’effacement permettent à l’entreprise de couper sa consommation électrique sur demande pour soulager le réseau national à des heures critiques.
Mora Group : vers un site 100 % électrique et renouvelable
Dans le Beaujolais, Mora Médical, filiale du groupe Mora International, a fait un pari audacieux : électrifier entièrement son site industriel, tout en basculant sur de l’électricité d’origine 100 % renouvelable. “Nos process, notamment l’injection plastique, sont très électro-intensifs. Depuis novembre 2024, nous fonctionnons uniquement avec de l’électricité renouvelable. Nos émissions directes de CO₂ sont désormais quasi nulles”, explique Alexandre Fontbonne, directeur industriel. Deux leviers ont permis cette bascule : le remplacement de 34 presses hydrauliques par des presses électriques, et la récupération de chaleur résiduelle pour tempérer les ateliers. Résultat : en quatre ans, la société affiche une baisse de 40 % du volume d’électricité utilisé, À ce score spectaculaire s’ajoute une réduction de 30 000 litres de sa dépense de fioul à l’année, soit l’équivalent de la consommation annuelle de 500 foyers. Ce projet a aussi transformé le quotidien des équipes. “Les presses électriques sont plus silencieuses, plus propres et nécessitent moins de maintenance. Cela améliore la qualité de vie au travail et réduit la pénibilité”, observe Rachel Roche, responsable RH de l’entité. Mora ne compte pas s’arrêter là. Un projet de centrale solaire devrait voir le jour dans les prochains mois, et le groupe vise une labellisation RSE engagée d’ici 2026. Selon la direction, il s’agit d’une démarche de fond, à la fois éthique, stratégique et économique. Ici, la sobriété, ce n’est pas une contrainte, elle est envisagée comme une solution d’avenir.
partager cet article
ON VOUS RECOMMANDE AUSSI
-
News
5 entreprises industrielles qui accompagneront votre été
04/08/2025
De la fabrication artisanale et high-tech aux matériaux innovants et durables, ces sociétés mêlent savoir-faire local et modernité pour vous accompagner pendant la saison estivale. De la…
-
News
Ouverture d’usines : 88 sites industriels inaugurés au premier semestre 2025
22/07/2025
Selon l’Observatoire Bpifrance des startups, PME et ETI industrielles françaises, la tendance est à la hausse pour les ouvertures d’usines et les investissements au premier semestre…
-
News
SHB Biotech : la première usine d’upcycling de la banane pousse en…
10/07/2025
Comment transformer le bananier en un levier de souveraineté pour la Martinique ? Il y a plus de dix ans, lorsqu’elle fonde un laboratoire spécialisé en recherche et développement…
-
News
Les ETI en 2025 : une dynamique verte qui résiste malgré un climat…
09/07/2025
La 15ᵉ enquête annuelle de Bpifrance Le Lab, menée auprès de plus de 600 entreprises de taille intermédiaire (ETI), révèle un contexte économique prudent pour 2025. Pourtant, malgré un…